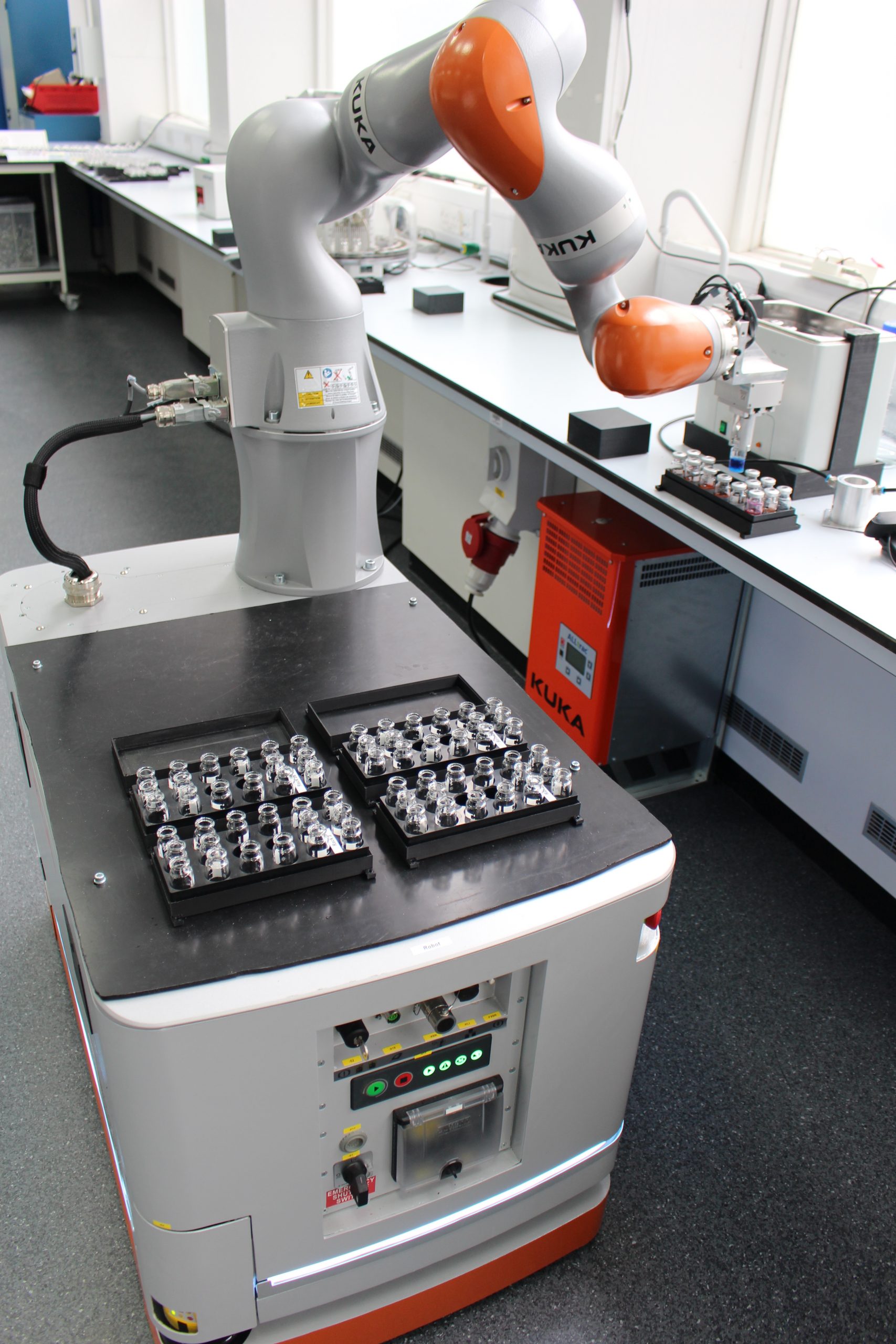
The fourth industrial revolution is rapidly transforming the UK’s manufacturing sector. Through harnessing the power of advances in AI, machine learning and virtual reality technologies, it’s a disruption built on digitalisation. However, to maximise its potential to drive economic growth, we must apply the principles of Industry 4.0 across the entire innovation value chain. By using robotics and high-performance computing to revolutionise the way in which research and development (R&D) is carried out, we’ve developed a ground-breaking approach for academia and industry – Innovation 4.0.
Innovation 4.0 aims to transform the scale, quality and impact of translational research by re-engineering the traditional innovation process in order to accelerate academic discoveries and commercial product launches. Currently, most R&D labs will rely on spreadsheets and lab notebooks to record manually produced data. Typically, a researcher working in a chemistry lab at a UK university will spend the bulk of their time investigating a narrow range of materials in detail, manually inputting experimental data into a computer for analysis. It’s labour intensive and leaves little time for experimental creativity.
By leveraging the digital technologies that underpin Industry 4.0, and applying them in the innovation process, traditional R&D is being transformed into Innovation 4.0. We are using the internet of things (IoT) to create digital lab benches which automatically capture everything a scientist does, without changing what they do. This helps them produce detailed experimental data sets with an increased resolution of what they actually did, compared to manual recording methods. This data is then automatically stored using cloud computing systems for more secure and effective data management. Automated workflow systems and co-operative robots (cobots) are being used in labs to perform long, high frequency tasks that humans cannot execute with high levels of reproducibility. Cobots reduce monotonous and repetitive work, and this partial automation of the R&D process provides scientists more time to think creatively about what the data is telling them and focus on how to reach their next big insight or discovery.
Machine learning and AI techniques are harnessing cutting-edge mathematical algorithms to provide R&D teams with deep scientific insights. This information is then used to publish results in high-impact journals, file patents, create new software platforms, and design and improve future research programmes. Also, digital twins are being used to design, create and simulate virtual experiments before they’re implemented in the real world for a fraction of the costs of traditional R&D. Applying these emerging areas of digital technology to traditional R&D processes, in combination with highly sophisticated feedback control loops, is creating the first generation of Innovation 4.0 research labs.
Recognising the importance of Innovation 4.0 for both academia and industry, the £81m Materials Innovation Factory (MIF) opened for business in late 2017 with a vision to be the world’s leading centre for computer aided materials science. Located in the heart of Liverpool’s thriving Knowledge Quarter, the MIF was co-founded through strategic innovation partnerships between the University of Liverpool, Unilever and UK Research and Innovation (UKRI). The MIF has since attracted funding from the Henry Royce Institute and a range of commercial partners. Through the integrated use of Innovation 4.0, we’re developing new approaches to advanced materials, chemistry and formulations, re-thinking potential applications and driving R&D into the 21st Century.
The MIF is an 11,600 m2 facility containing one of the world’s largest collections of scientific equipment for materials chemistry research. The building is ‘open by design’ and its labs are available for use by academics and industry specialists alike, with a dedicated team of technical experts available to assist with experiments and train scientists on how to use our cutting-edge kit. We provide a unique template for translational research, bringing together world-leading material science, some of the world’s biggest multinational companies, and a suite of dynamic SMEs from across the local and national chemical industry to create a diverse Innovation 4.0 ecosystem. The MIF also houses Royce @ Liverpool, our contribution to the £235m Henry Royce Institute, bringing together the University of Liverpool with eight other leading research organisations across the UK to create a national centre of excellence for advanced materials.
The academic expertise of the University of Liverpool is at the heart of the MIF. The University has the second best chemistry department for world leading research in the UK according to last Research Excellence Framework process, with 99% of our outputs ranked as either world leading or internationally excellent. The MIF is home to a number of the most pioneering and highly decorated materials scientists and chemists of our generation. Professor Andy Cooper, a Fellow of the Royal Society and a world leader in the area of computer-aided materials discovery, is using cobots and high-powered computing systems in the MIF to accelerate the creation of materials for a variety of applications including energy capture and storage.
Another Fellow of the Royal Society, Professor Matt Rosseinsky, is a pioneer in the design and discovery of solid state materials, which have wide-ranging applications, from catalysis to superconductivity. Professor Rosseinsky and his research group are using the facilities available in the MIF to develop new methods of identifying functional materials, with a focus on integrating their experiments with the latest computational methods. Researchers in the MIF are also interested in the medical applications of materials chemistry. Professor Steve Rannard is applying novel polymer chemistry and organic nanoparticle production to the field of nanoscience to combat infectious diseases such as HIV.
The MIF is a dynamic and growing Innovation 4.0 ecosystem, creating a crucible for accelerated scientific discovery and future economic growth for the UK. The potential that new, large scale aggregations of automation, control and cognitive computing can offer academic and commercial R&D is simply limitless.
To learn more about Innovation 4.0 and the MIF, visit: www.liverpool.ac.uk/materials-innovation-factory